PepsiCo Bottle Design, 3D Printing
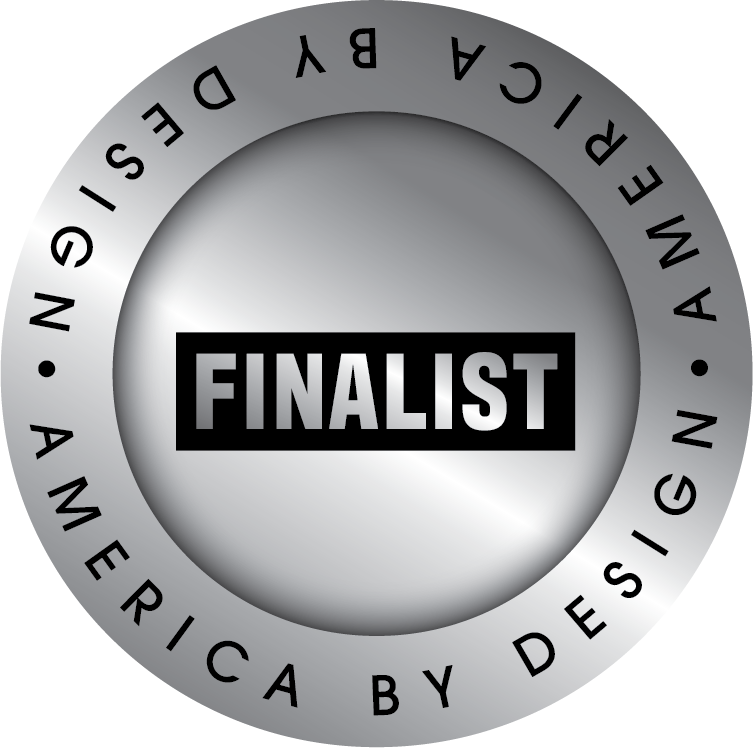
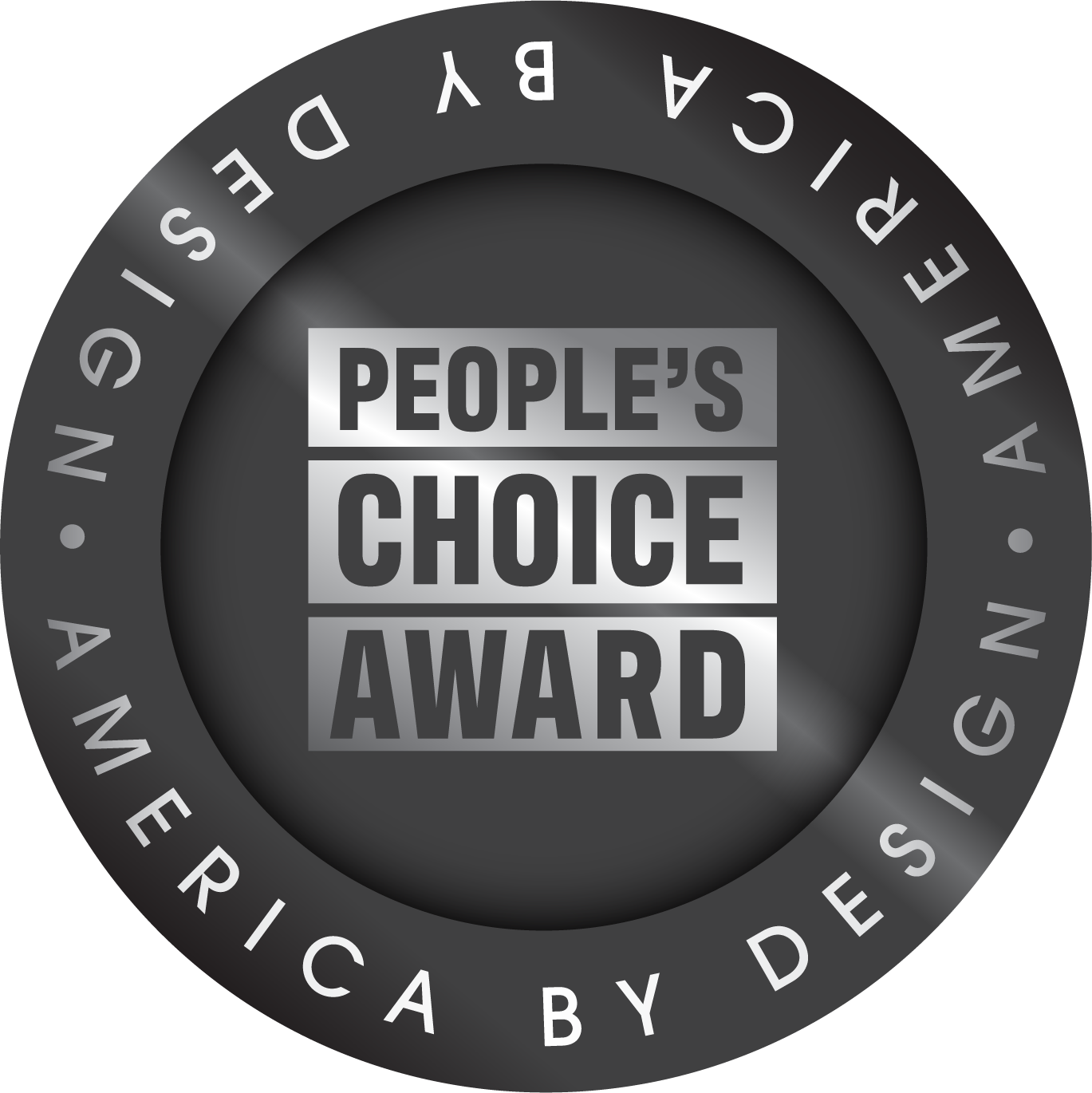
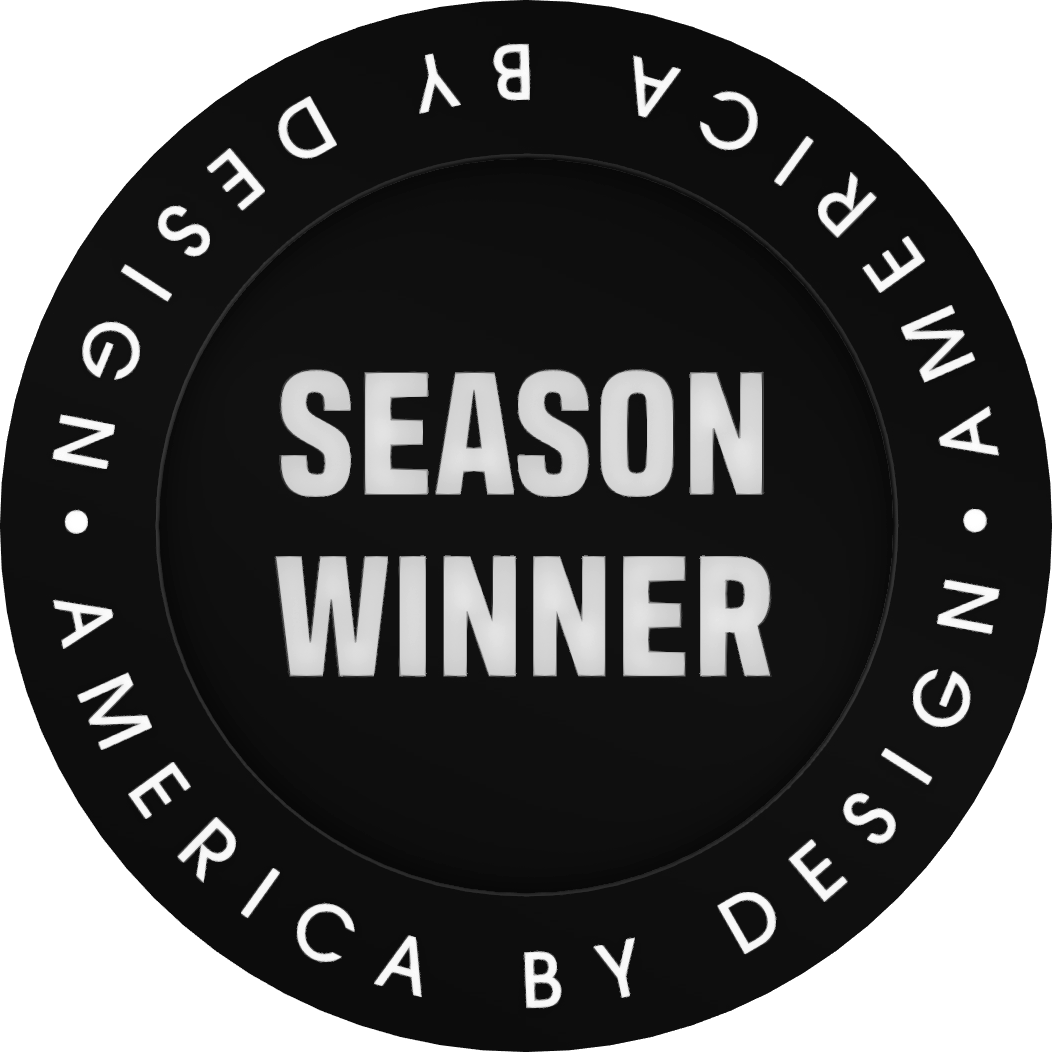
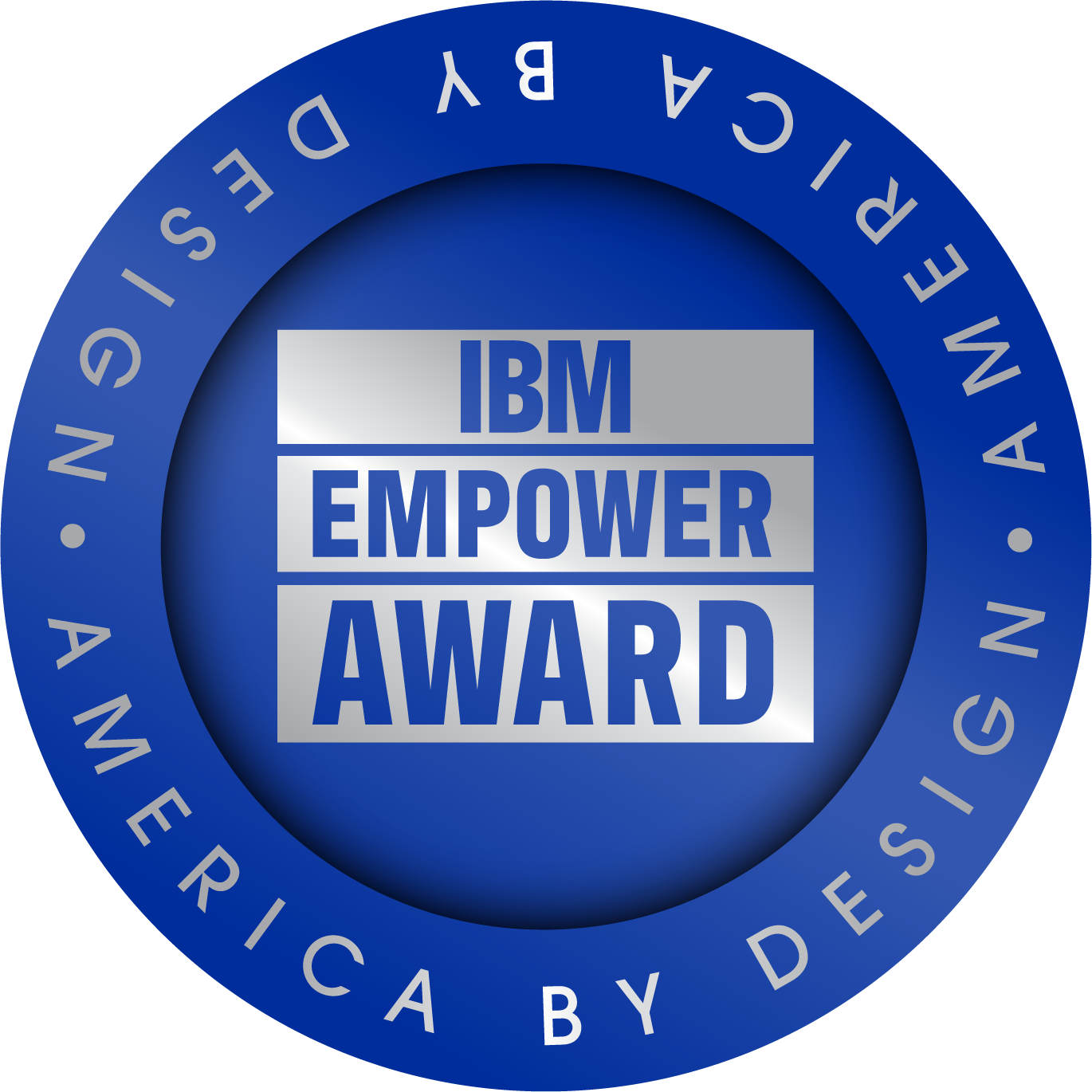
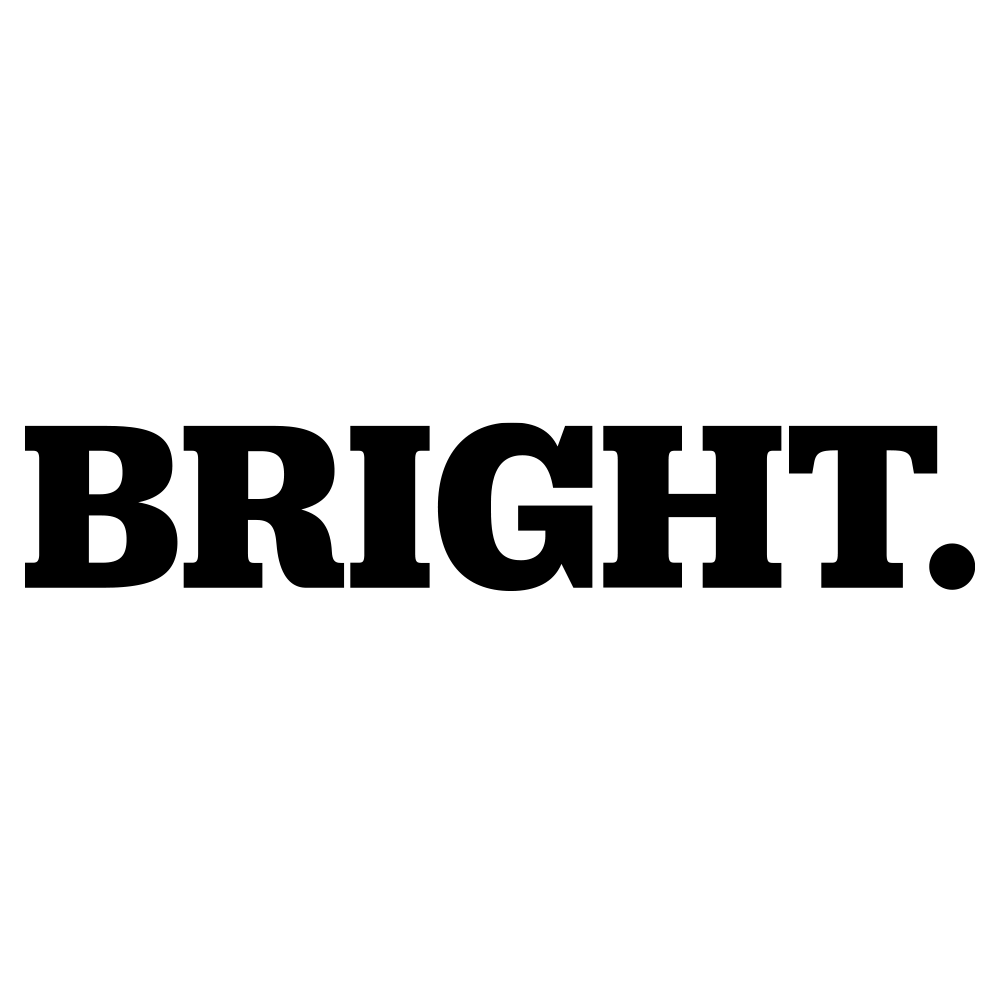
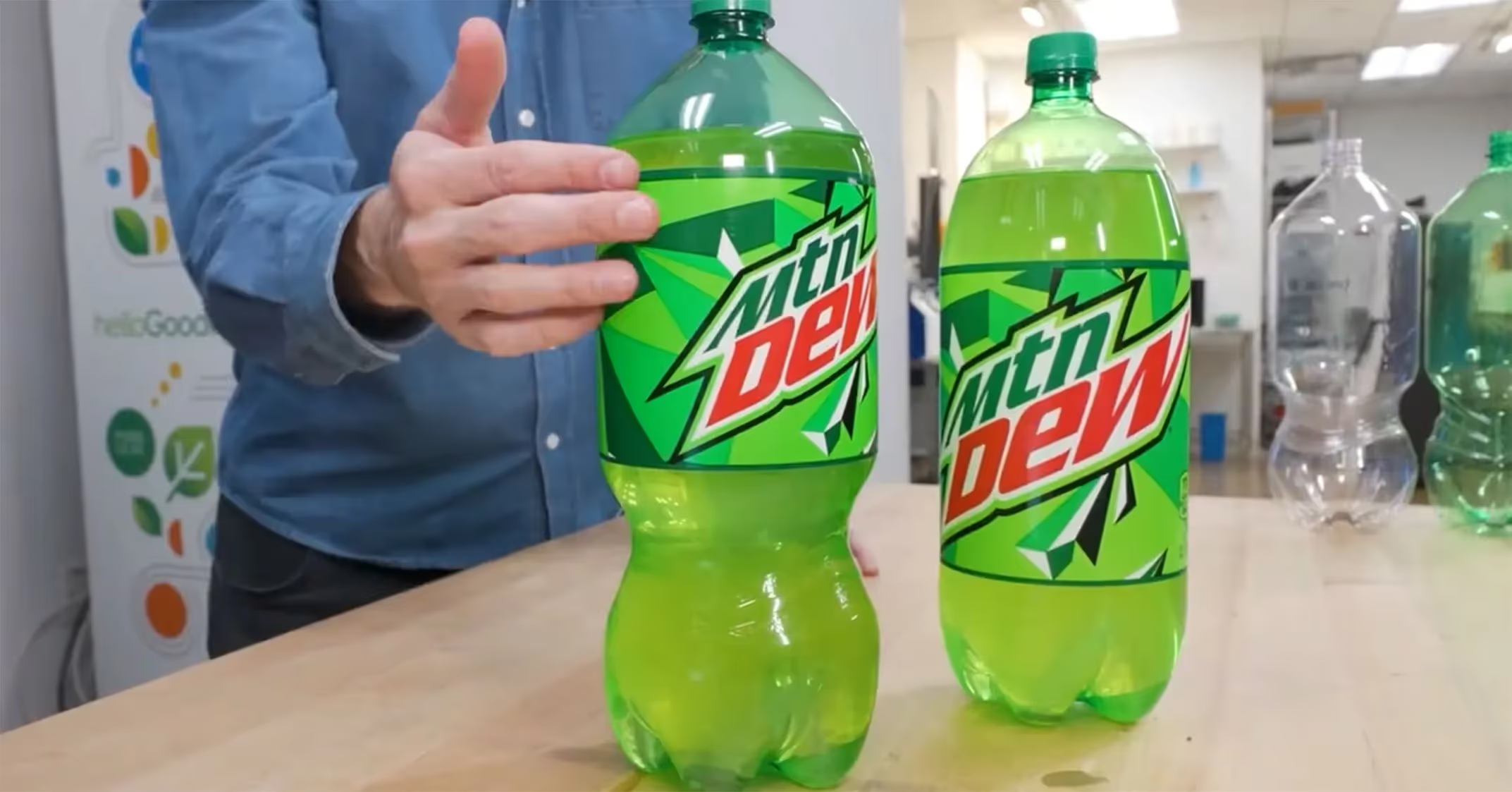
PepsiCo’s Structural Packaging Design and R&D teams have reinvented their workflow using the latest advances in 3D printing technology.
Designers and engineers spend a significant amount of time translating sketches into prototypes to land the best design for consumers, while ensuring the new designs also conform rigorous technical constraints.
They can now provide a better result in far less time.
PepsiCo’s 2L PET bottle re-design demonstrates how the combination of physical and virtual simulation gives confidence in the overall design before committing to invest in the upgrade. First, designers work on-screen to craft dozens of models that are quickly 3D printed in a bare monochrome color to evaluate ergonomics and overall proportions. Next, a computer-based simulation is used to predict how the bottle shape will change once the internal pressure is applied, as carbonated bottles often contain more pressure than a typical car tire!
A new, full-color 3D printer (the Stratasys J55) now allows the team to quickly make photorealistic bottle prototypes in-house that accurately demonstrate the final textures, colors, and label design. These prototypes help communicate the design to cross-functional stakeholders to gain alignment much more quickly and cost effectively than traditional 3D prototyping methods requiring external vendors.
Finally, the team takes this process a step further by 3D printing mold cavities in-house, which enables them to blow-mold bottles that can be tested on the lab production line.
"We found the way over the years to invest in new technologies and methodologies is not about the product itself, it is about the design of the process" - Mauro Porcini
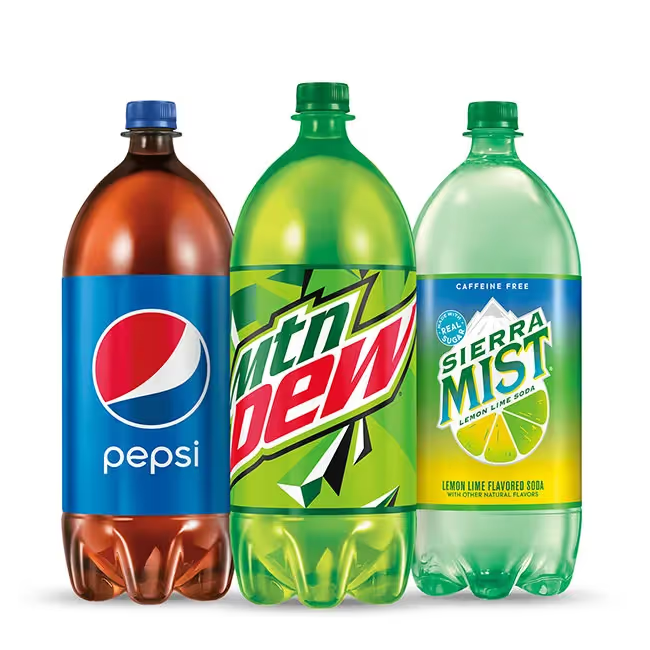
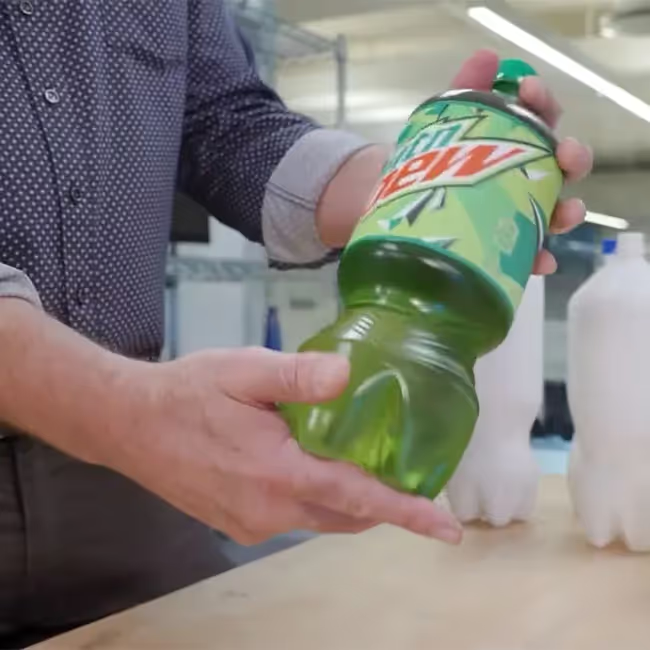
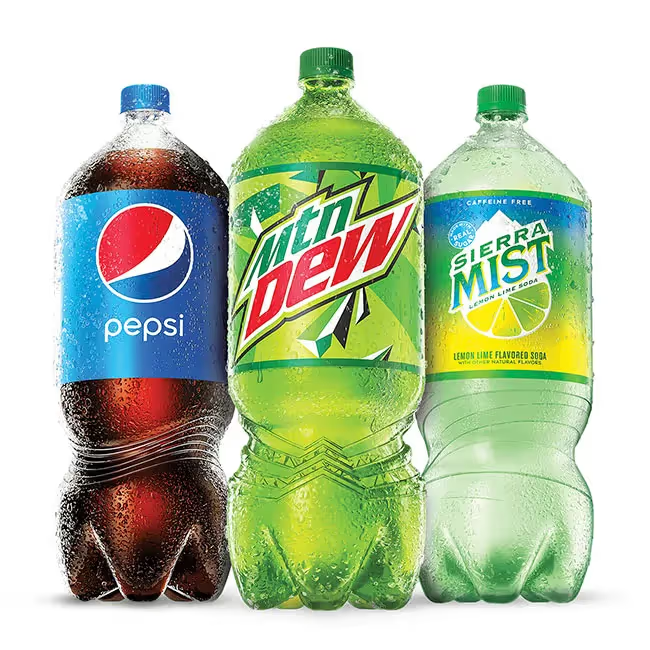